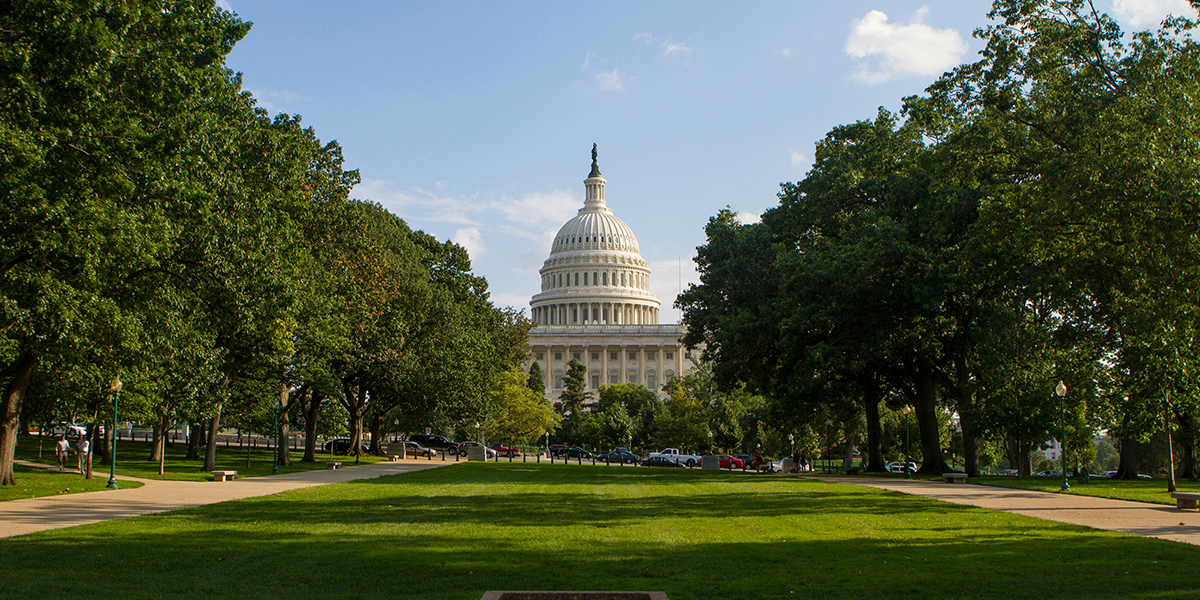
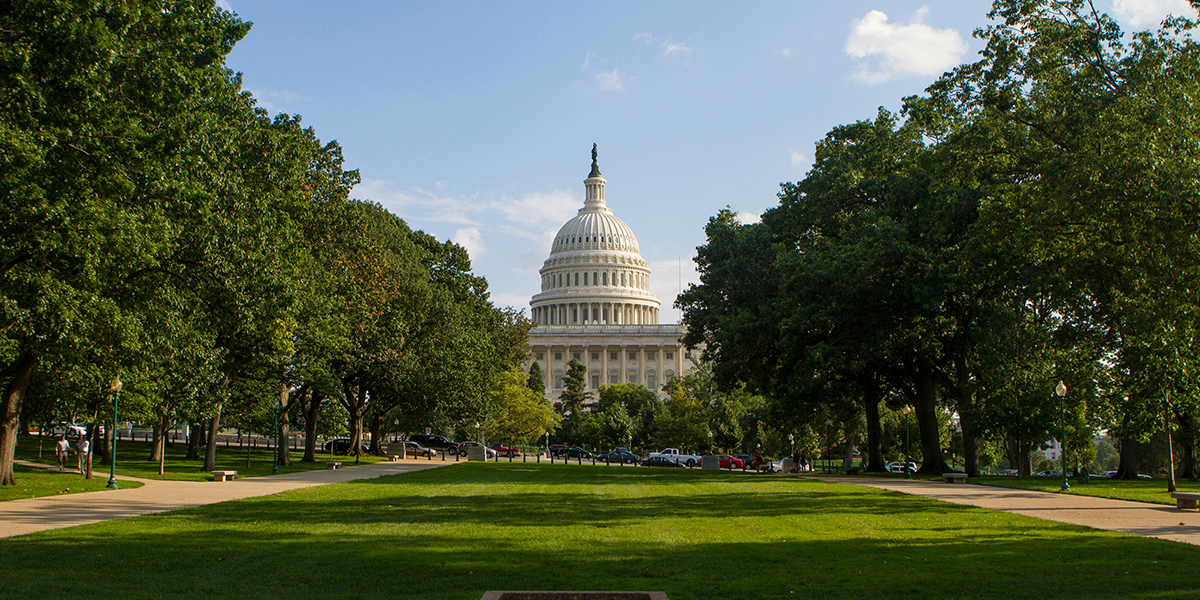
Blog
Many of us in the building industry believe that, combined with a good continuous air seal, the highest insulation value makes the greenest enclosure, helping to reduce a structure’s carbon footprint and combat climate change. It may come as a surprise, then, that some of the most commonly used insulation materials are so carbon-heavy to manufacture and/or install, that for many decades they wipe away the carbon-energy savings they are supposed to provide.
SWA’s Enclosure Group is acutely aware that insulation is the most important single material choice to maximize the enclosure’s thermal resistance over its operational life. Many of us in the building industry believe that, combined with a good continuous air seal, the highest insulation value makes the greenest enclosure, helping to reduce a structure’s carbon footprint and combat climate change. It may come as a surprise, then, that some of the most commonly used insulation materials are so carbon-heavy to manufacture and/or install, that for many decades they wipe away the carbon-energy savings they are supposed to provide. The following is a detailed discussion of how and why this is, and what the industry is doing to change the equation.
The built environment looms large in the climate picture, because almost 40% of the total carbon put into the planet’s atmosphere each year is attributed to buildings. Over the past 30 years of green building, we have overwhelmingly focused on operational carbon – the carbon that buildings emit as they are being used. Only recently have we begun to focus on embodied carbon – the carbon that goes into constructing buildings, which is typically far greater than the energy saved in the first decades of operation. Changes in energy codes are aimed at operational carbon, and even those organizations and standards that have been at the forefront of promoting sustainable building [LEED, PH] have not been quantifying or limiting embodied carbon, although they bring attention to it.
Assuming that a building stands for many decades, or even centuries, its operational carbon will eclipse its embodied carbon over its lifetime, and therefore when the building’s carbon Life Cycle Assessment (LCA) is calculated, operational carbon savings will be more important than embodied carbon saved/spent in the long run. Why does embodied carbon deserve equal weight with operational carbon? Because of the total global carbon emissions from buildings, 28% is pegged to embodied carbon. That’s already a large percentage, but when you consider the near term, the first 30 years of a building’s life, the percentage jumps to about 50%. In effect, every new building is in carbon debt upon completion due to the huge amount of carbon emitted in order to construct it., And in order for the climate to benefit from the energy savings provided by a well-insulated and sealed enclosure and a high efficiency energy system, the building needs to last and be used for a very long time. The problem is that we may not have 30 years, let alone 60, to pay off that carbon debt.
There are varying projections as to when the rise in global temperature due to the amount of carbon in the air might reach a tipping point and trigger a set of cascading climatic events with catastrophic consequences. Most projections are in the relatively near term – 10-30 years. That means we can no longer afford to make choices that have us paying off a carbon debt decades into the future. The atmospheric carbon level is now nearly 410 ppm. According to the Bloomberg Carbon Clock, in 20 years it may reach 450 ppm, the predicted trigger level. These are absolute numbers, so every bit of carbon we put into the air right now counts.
We are not suggesting that we should now shift focus away from reducing operational carbon and focus primarily (or exclusively) on embodied carbon. On the contrary, the lower the operational carbon emissions, the quicker the carbon debt is paid off. Thermal insulation is therefore critical to a building’s ability to pay off its debt. Conversely, the lower a building’s embodied carbon, the more effective its operational efficiency really is. The two values are inseparable. When design seeks to minimize both types of emissions, the resulting buildings can radically reduce carbon emissions, contributing to a reduction in atmospheric carbon that can lead us away from the tipping point.
The primary purpose of thermal insulation is to provide resistance to heat transfer through the building enclosure, typically quantified as R-value. The higher the R-value, the better the insulating property. Except in cases where a building is mostly glass curtainwall, insulation is the main determinant of the potential R-value of any enclosure surface – floor, wall, and roof. There are too many insulation materials on the market to discuss all of them here. With respect to commercial construction in the NYC area, overall there are three types of materials in common use:
The highest R-values(5 or 6.5/inch)are associated with plastic foams. Mineral fibers tend to max out at R4 per inch, while organic fibers are somewhere in the R3 range. All other things being equal, you want to have the highest R-value per inch, but it’s not that simple. Many other factors have to be considered, even without considering embodied carbon.
It turns out that two of the plastic foams that provide the highest R-value – closed-cell polyurethane spray (SPF-HFC type) and extruded polystyrene board (XPS) – also have the highest embodied carbon; not by a little but by several orders of magnitude. This is because they are both made with a hydrofluorocarbon (HFC) blowing agent that has upward of 1000 times the global warming potential (GWP) of carbon dioxide. A study found that the time it takes for the operational carbon savings from HFC blown XPS or SPF to pay back the emissions from their fabrication and installation can range from 40 to 60+ years, depending on total R-value provided between R10 and R25. If the insulation takes that long just to pay for itself, it’s not starting to pay for any of the other embodied carbon. In commercial buildings, the insulation is typically a minor proportion of the embodied carbon for the building – as low as 5-10%. That means that around 90% of the building won’t begin to realize carbon savings from insulation until after 40 or 50 years of operation, at a minimum.
By contrast, the same study found that for the same R-value, the range of payback for any of the other types of insulation, including plastics blown with agents other than HFC, is between one and four years. From the standpoint of embodied carbon alone, it is hard not to conclude that HFC blown plastics should be phased out and taken off the market as quickly as possible. But SPF and XPS insulation are ubiquitous, and it’s not only their high thermal performance that makes them so popular. We have become dependent upon SPF and XPS because they do so many things in addition to providing high R-value.
For all practical purposes, XPS board is waterproof and serves as a vapor barrier. If taped and sealed, the boards are an air barrier. Therefore, this insulation type can take the place of a vapor barrier or an air barrier in a wall assembly. And, with various levels of compressive strength, from 25psf to 100psf, it has real structural value as well. XPS board is often used as a protection board for membranes and is the go-to insulation for foundation waterproofing because of its long-term ability to stand up to hydrostatic pressure. Moreover, it is dimensionally stable, and has good long-term R-value retention.
Closed-cell SPF is likewise highly water resistant, although not to the same degree as XPS (under hydrostatic pressure). And, closed-cell SPF is an even better air barrier, since as a spray applied material it conforms to all kinds of irregularities and is seamless. When installed at minimum 1.5” thickness, it is also a Class I vapor retarder. Sprayed on SPF becomes so rigid when set that it can provide structural rigidity, if desired, in some wall systems. Similar to XPS, it is dimensionally and thermally stable.
None of the other insulations, even the non-HFC blown plastics, completely replicates all the characteristics of HFC blown SPF and XPS. Plastic foams generally are highly flammable and are not the best fit for every application, but how can we make up for the loss of the combination of helpful qualities that has made us so broadly dependent on them?
Read on to Part 2 to find out!
Contributor: Catherine Paplin, Senior Building Enclosure Consultant
Steven Winter Associates